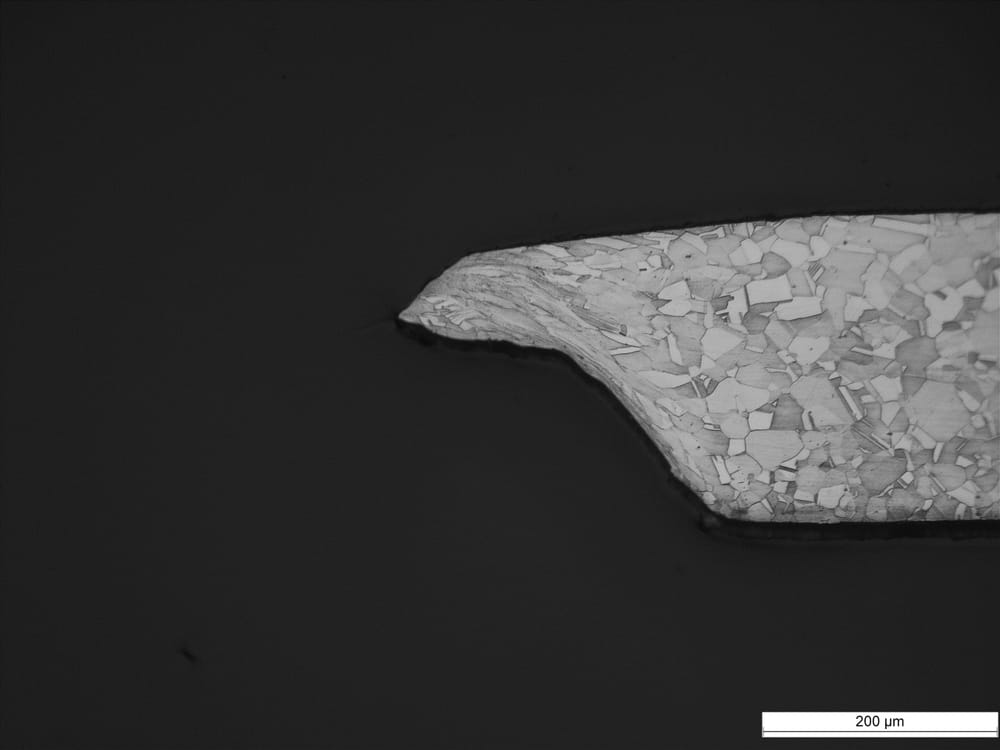
At first glance, Monel® (a trademark name that refers to several different alloys) looks a lot like chrome-molybdenum steel, and there are some overlaps in how these alloys are used, for instance, in highly corrosive environments. However, Monel is a nonferrous alloy of nickel and copper with some unique properties….