Water supply, oil and gas, chemical, and other critical industries rely on pipelines to provide essential infrastructure for their successful operation. And because these pipes must withstand high pressure and harsh conditions, they require the highest quality materials and processes. Likewise, operators must optimize weld parameters to achieve ideal efficiency—especially when welding large-diameter, thick-walled pipes. Because seamlessly welding these pipes can be difficult when welding manually, manufacturers have implemented automatic pipe welding machines for reliable, high-quality welds and increased productivity.
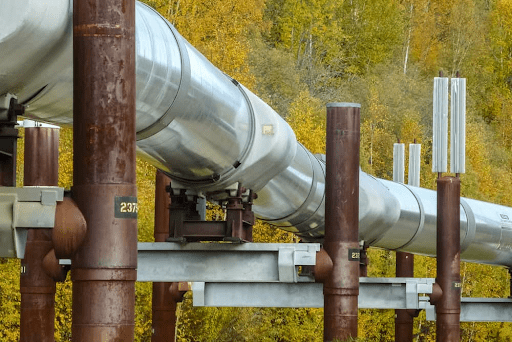
Efficient Pipe Welding: Manual Vs. Automated Welding
Critical pipeline welding cannot tolerate a large margin of error; therefore, this welding requires highly skilled operators to perform quality welds. However, as the bore diameter and wall thickness increase, welding difficulty also increases.
Manual Pipe Welding Challenges
To ensure pipe welding consistency, operators should weld continuously around the pipe with controlled arc, feed, heat input, and speed. However, even for welders with years of experience, “human error” is possible. Additionally, large-diameter, thick-wall piping is impossible to weld in one continuous pass. Resulting inconsistencies can give rise to weld defects such as lack of penetration, inclusions, cracks, porosity, undercutting, splattering, and more. Factors that contribute to manual pipe welding challenges include:
- Welding environment: limited accessibility, insufficient weld head clearance, lack of visibility, overhead welding position.
- Safety: the presence of radioactive elements, high exposure to carcinogenic fumes like hexavalent chromium when welding stainless steel pipes, fatigue due to continuous welding.
These challenges can affect weld quality and manufacturing productivity. Manufacturers also face an industry-wide challenge resulting from the current welder shortage. Studies suggest the need for around 375,000 welders by the end of 2023.
In response to these challenges, industries are increasingly implementing automated welding systems like orbital welding.
Orbital Pipe Welding
Automated welding systems such as orbital TIG (Tungsten Inert Gas) have gained popularity among pipe welders and manufacturers for their consistent and reliable weld results. For pipe-to-pipe welding of large or small bore pipes, orbital welding offers:
- Weld parameter control
- Remote monitoring and optimization ability
- Smooth and consistent weld bead
- Purity in weld results
- Repeatability
These orbital welding attributes help provide safe and efficient welding options for critical pipeline system technicians.
Automation Offers a Productive Pipe Welding Solution
Automatic pipe welding machines facilitate orbital welding for a wide range of pipe diameters and thicknesses. These machines are especially beneficial for pipelines in the petrochemical, construction, or water engineering industries where large diameters and thick walls must withstand extreme stress and pressure.
Inside diameter welding presents a significant issue when welding pipes with a larger diameter. When welding manually, often welders must crawl inside the pipe to perform the weld. Automatic pipe welding machines with advanced orbital weld heads for internal diameter—like Model 15 from Arc Machines Inc.—facilitate a much simpler welding process. These weld heads can be mounted on a track along the internal diameter of the pipe, which can be controlled and monitored using a remote pendant to facilitate monitoring and weld parameter optimization throughout the welding process.
Similarly, for thick-walled pipes, multiple passes may be required to complete the weld. Automatic pipe welding machines facilitate controlled heat input, consistency, and precision in each pass. The repeatability offered by the automated welding machine allows uniform pipe welding without any break during the welding process. The continuous process without the “fatigue factor” helps produce high-quality welds with adequate penetration for high-stress applications.
Automatic pipe welding machines improve time savings, safety, and cost-efficiency. These characteristics can become deciding factors for manufacturers when selecting the appropriate welding process for their application.
Resources: Automated Pipe Welding Machines
Pipe welding is a critical process that requires attention to many intricate details. When determining the best pipe welding system for your application, explore these resources to discover the benefits of an automated orbital welding system.
- Big Bore Pipe Welding: Choosing Orbital Welding Systems for Large Diameter Piping
- Why Orbital TIG Is the Best Welding Type for Pipeline Applications
- What Is the Narrow Gap Welding Process and Why Is It Used?
- Key Advantages and Disadvantages of Orbital Welding
- GTAW Automated Pipe Welding Systems
- Overhead Pipe Welding: How Orbital Welding Simplifies a Difficult Position
- The Benefits of GTAW Wire Feed Pipe Welding for Your High-Spec Project
- When to Use Orbital Welding
- What Is the Best Way to Weld Pipe?
Automatic Pipe Welding Machines Improve Quality
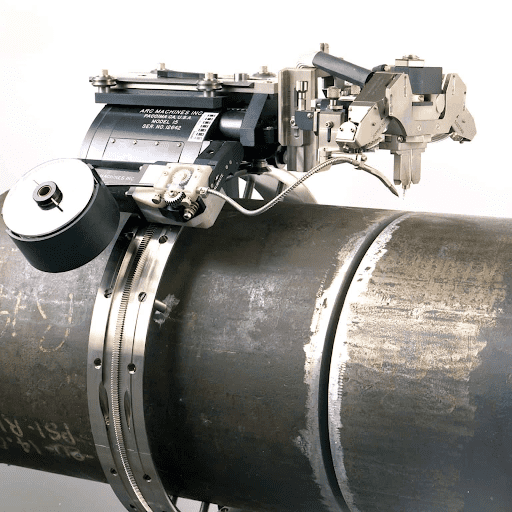
As pipeline construction expands to facilitate the global demand for water supply and petroleum access, it is more important than ever to find an ideal welding solution that provides quality results and minimizes maintenance. Orbital welding offers pure, consistent, and high-quality weld results to meet manufacturers’ needs across industries. Provisions for weld parameter control and monitoring capability enable precision welding for a wide range of pipe diameters and thicknesses. Additionally, the optimized and automated orbital welding process can increase cost-efficiency and improve productivity. By adopting automatic pipe welding machines, companies can ensure their pipeline projects display efficient, consistent, and reliable welds with unmatched quality.
READY TO CONNECT?
Arc Machines, Inc. specializes in orbital welding systems, offering weld heads and power supplies compatible with automatic pipe welding machines to help support your demanding petrochemical, construction, and other industrial welding projects. For inquiries regarding products, contact sales@arcmachines.com. For service inquiries, contact service@arcmachines.com. Contact us to arrange a meeting. Arc Machines welcomes the opportunity to discuss your needs.