As industries increasingly employ technology to improve efficiency and productivity, the welding industry has invested in collaborative robots to reduce costs and accelerate processes. Pairing robot efficiencies with human oversight in the welding process has yielded profitable solutions for the manufacturer.
Collaborative robots like AMI weld heads provide flexibility and accuracy in the automated welding process. Here are some of the benefits associated with collaborative robot welding.
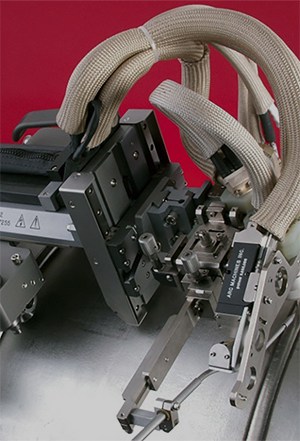
Advantages of Robotic Collaboration in Welding
Collaborative robots, also known as cobots, take advantage of robotic capabilities and human intelligence in the workspace. Industrial settings benefit from robot-driven consistency and productivity. In welding applications, robots provide high-quality output with faster production speed and reduced waste. Human collaborations with robots aim to ensure smooth functioning processes and performance. Human-robot interactions in welding provide the following benefits.
Accuracy and Precision
Collaborative robots are uniquely designed for delicate tasks like welding. Automated robots can adapt to varied welding settings and perform welds with constant speed. By increasing weld consistency, robots allow manufacturers to reduce the rate of rejection in the production process.
Product rejection may result from anomalies in the welding process. Integrating human oversight with the automated welding process manufacturers can further reduce defects resulting from anomalies in the welding process. The combination of robot-driven consistency with the welder’s pattern recognition capability offers the best possible solution to ensure profitable welding.
Safety
In collaborative robot welding, the most repetitive and exhausting work is performed by automated robots. Robot flexibility allows them to weld complex geometries that would have been difficult—and dangerous—for their human counterparts. And by working in close collaboration with robots, welders can concentrate on weld quality without being exposed to harmful fumes and gases, arc flash, or hot metals. Likewise, weld operators can optimize current or arc length without being exposed to health and safety risks.
Productivity through Optimization
Robotic welding comes with the advantage of optimization through programming. Some technology also allows real-time adjustment in robotic weld motion. Operators can program, optimize, and control welding parameters to achieve a high degree of precision and remove process waste while simultaneously monitoring multiple operations. Additionally, constant weld parameter monitoring reduces rework and the rate of rejection. And by continuously producing high-quality welds, collaborative robot welding increases both productivity and profits.
Integrating collaborative robots with orbital gas tungsten arc welding (GTAW) offers several advantages.
Orbital Welding With Collaborative Robots
Orbital welding is a semi-automated welding process. The automated weld head is used along with some level of human collaboration to perform the weld. As the automated weld head moves around the stationary pipe or tube , operators constantly monitor the welding process for any deviation that would require intervention. Adjustments can be made using a remote weld pendant. This collaboration improves efficiency in welding and increases productivity.
Collaborative robot performance is further enhanced with Internet of Things (IoT) integrations. Not only does IoT allow data capture and storage, but it also assists in real-time monitoring and defect detection. Operators can immediately identify bottlenecks in the process and address them to improve production efficiency. The future of smart welding will likely join collaborative welding with IoT.
Orbital Collaborative Robot Welding for Your Future Designs
Automated weld heads from Arc Machines, Inc. (AMI) allow industries to leverage the benefits of human-robot collaboration for orbital gas tungsten arc welding (GTAW). The processes that demand repetitiveness, precision, high-quality, and accuracy—such as the heat exchanger tubing process—can leverage the advantages of collaborative robot welding in their production process. The combination of humans, collaborative robots, IoT, and data analytic is destined to shape tomorrow’s manufacturing process.
READY TO CONNECT?
Arc Machines, Inc. products for orbital collaborative robotic welding provide consistency and improve productivity for pipe or tube welding applications. For inquiries regarding products, contact sales@arcmachines.com. For service inquiries, contact service@arcmachines.com. Arc Machines welcomes the opportunity to discuss your specific needs. Contact us to arrange a meeting.