A term that is often used or perhaps overused is welding quality. Well, what exactly does welding quality mean? The fact is there is no single answer. For a weld to truly be of sufficient quality, it must meet the demands of its application. For pressure vessel welding, this means exhibiting sufficient strength and reliability to avoid cracking, softening, or breach of any kind during operation. These same attributes apply to the welding of pressure vessel nozzles, which are the essential links from the vessel for inflow from and outflow to the industrial piping system.
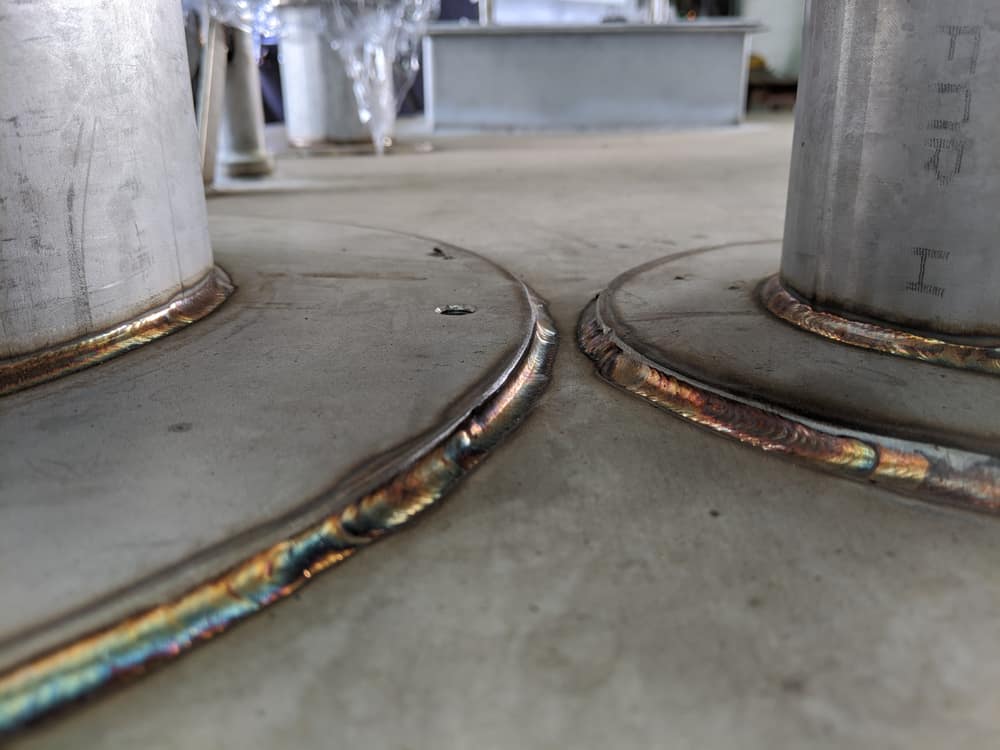
What Is a Pressure Vessel Weld Nozzle?
Pressure vessel nozzles typically have two or three parts or sections:
- The flange that connects to the external pipe
- The neck
- The reinforcement at the vessel (if necessary)
Knowing how to best weld pressure vessel nozzles requires an understanding of the different types of nozzles used with boilers, heat exchangers, and storage containers.
Pressure Vessel Nozzle Types
- Radial – Nozzle is perpendicular to the vessel surface, and nozzle neck height or distance from the vessel surface is the same around the nozzle neck-surface or reinforcement connection.
- Non-radial – Nozzle neck distance to the vessel surface varies around the nozzle neck surface or reinforcement connection. Examples include the following:
-
- Angular nozzles
- Hillside nozzles
- Tangential nozzles
- Head – Nozzle is connected at one of the vessel ends.
- Shell – Nozzle is connected to the vessel body or shell instead of the end.
In addition to the above types, vessel nozzles may also be classified as described below:
- Set-in where the nozzle projects into the vessel surface and the vessel opening diameter coincides with the OD of the nozzle neck.
- Set-on where the nozzle is on the vessel surface and the vessel opening coincides with the ID of the nozzle neck.
Nozzles may also be self-reinforced, or they may require an additional plate to assist in external loading on the nozzle. Irrespective of the nozzle type, there are weld requirements that must be met.
Nozzle Weld Requirements for Pressure Vessels
The manufacturers of pressure weld nozzles set the loading capacity for their products. These designs are guided by standards and codes.
Common Codes for Pressure Vessel Nozzle Designs
- ASME BPVC Section VIII
- British Standards Institute (BSI) EN-13445
- BSI PD 5500
- A. D. Merkblatt Code
- GB-150-2011
When welding of these nozzles, specific attributes, as listed below, are required to ensure the integrity of the pressurized system applications.
Pressure Vessel Nozzle Weld Essential Characteristics
- Strength
- Corrosion Resistance
- Thermal resilience
- Pressure resilience
To consistently meet the requirements listed above for pressurized systems, manufacturers should utilize the best available welding process, techniques, and equipment.
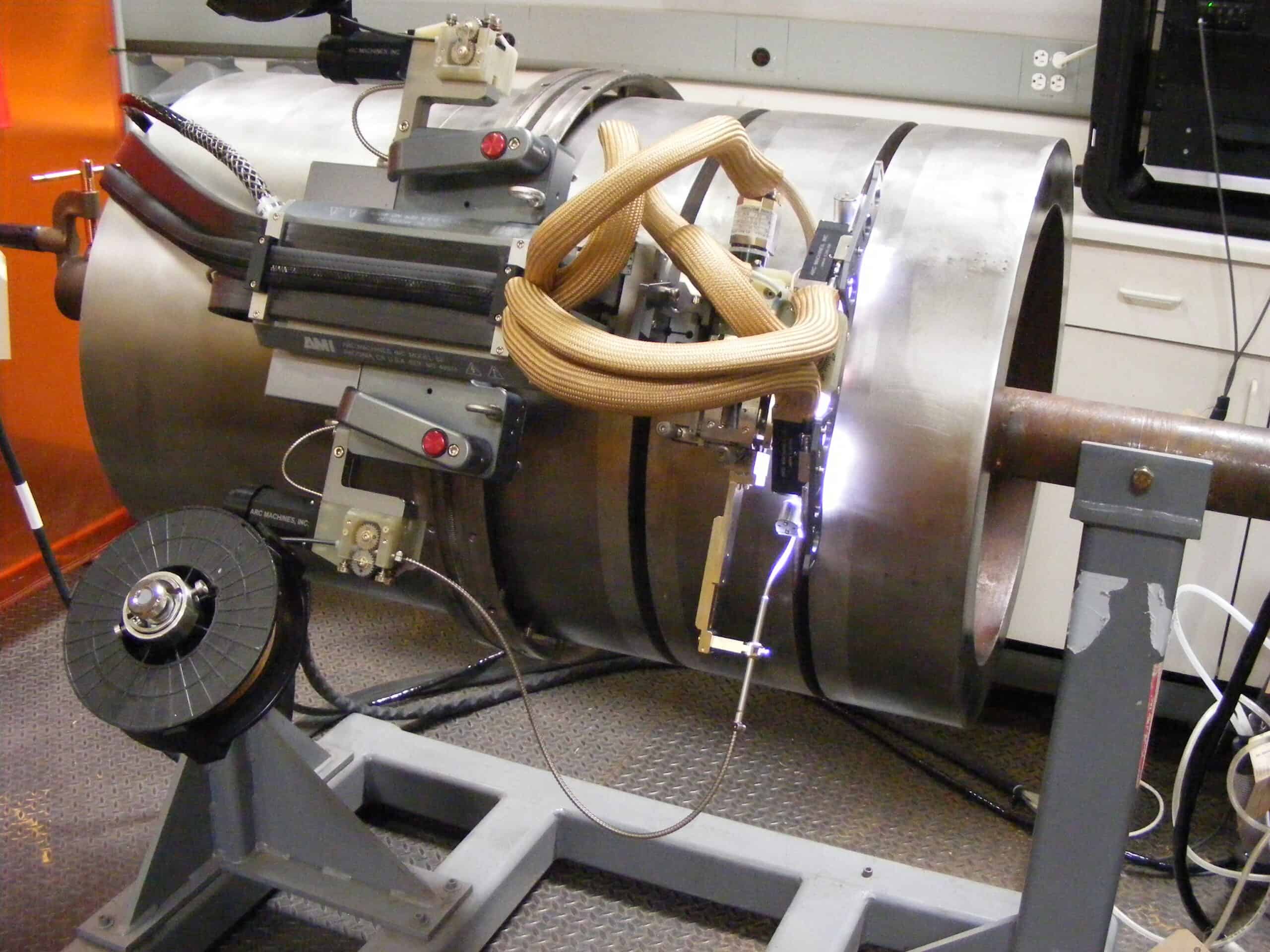
Creating the Highest Quality Nozzle Welds for Pressure Vessels
Performing high-quality pressure vessel nozzle welding means creating strong, corrosion-resistant, thermal, and pressure resilient connections that can withstand the rigors of their industrial environment. Because working in these environments can often be hazardous for welders, manufacturers should prioritize safety during assembly (as well as for post-construction workers and the environment).The best way to satisfy these objectives and meet the quality requirements is to employ an orbital welding service.
The Advantages of Orbital Welding for Pressure Weld Nozzles
Consistency
The most important characteristic in producing strong welds—aside from the material used—is the consistency of the weld generation, which automated orbital welding optimizes.
High Quality
Orbital welding lends itself to the highest quality welding techniques, including GTAW.
Efficiency
The creation of high-quality, consistent welds means fewer or no repairs, less wasted materials, and extra time. These advantages contribute to greater efficiency and higher project ROI.
Safety
Automated orbital welding removes the welder from proximity to the weld puddle and the toxic fumes that are likely present for pressure vessel piping systems.
When looking for an orbital service that includes the best equipment, materials, and support, the choice is AMI.
READY TO CONNECT?
Arc Machines, Inc. is an industry leader in supplying advanced and high-quality welding equipment and service. This includes expertise, welding machines, materials, and orbital weld heads to aid you in meeting the requirements of pressure vessel nozzle applications, regardless of industry. For inquiries regarding products, contact sales@arcmachines.com. For service inquiries, contact service@arcmachines.com. Arc Machines welcomes the opportunity to discuss your specific needs. Contact us to arrange a meeting.