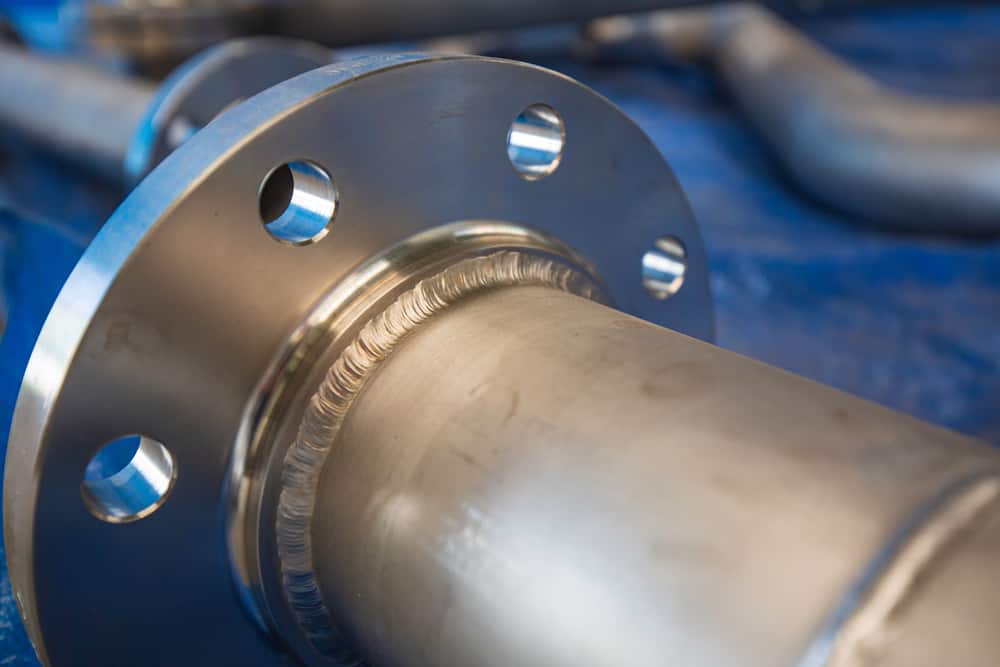
Materials in the oil and gas industry (and other chemical processing industries) should offer resistance to corrosion, high temperature, and high pressure. Additionally, they should possess excellent strength characteristics and be easy to fabricate. Carbon steel has been the industry standard for piping and tubing, but it can be corrosive…