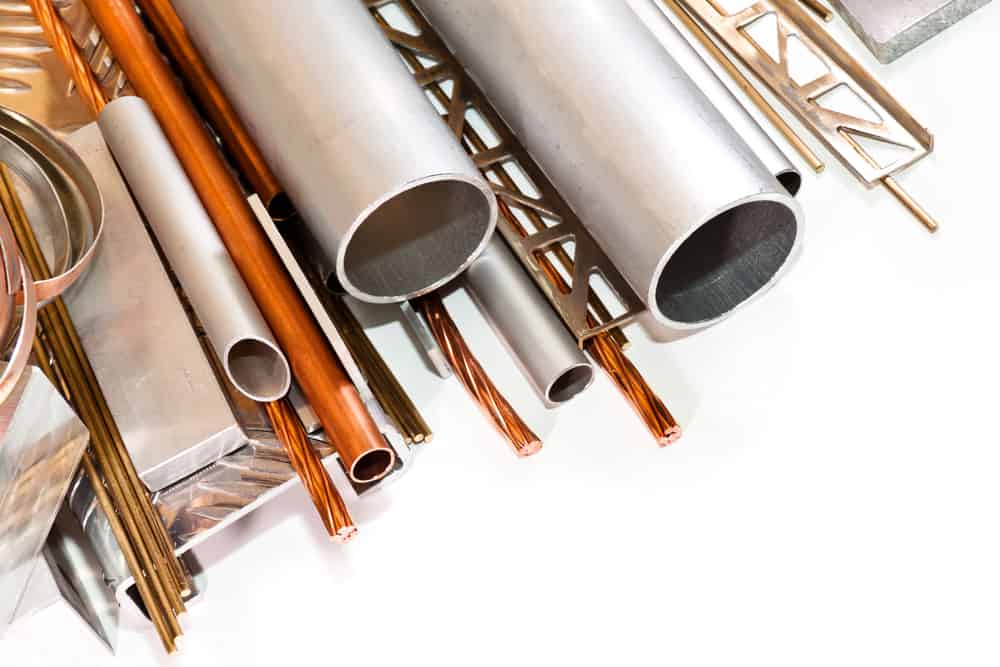
Thin or thick sections, steel or aluminum, TIG welding can join it all. And the fusion ability is not just limited to the material with closely-related properties, but it also extends to dissimilar metals. Creating a reliable bond when the properties of two materials differ drastically is challenging, but much…