The history of orbital welding dates back to the 1960s when it was first implemented to mitigate fluid leaks in the famous X-planes series of experimental aircraft. Since then, the process has been used in rockets, commercial passenger aircraft, petrochemical industries, semiconductors, and biopharmaceuticals. The unique properties and benefits of orbital welding — along with processes such as Metal Inert Gas (MIG), Submerged Arc Welding (SAW), Flux Core Arc Welding (FCAW), and laser beam arc welding — soon extended to industries beyond aviation. However, Gas Tungsten Arc Welding (GTAW) continues to yield welds of superior strength and quality. Below, we detail the types of orbital welding, the benefits and components of GTAW orbital welding, and its continued popularity across industries.
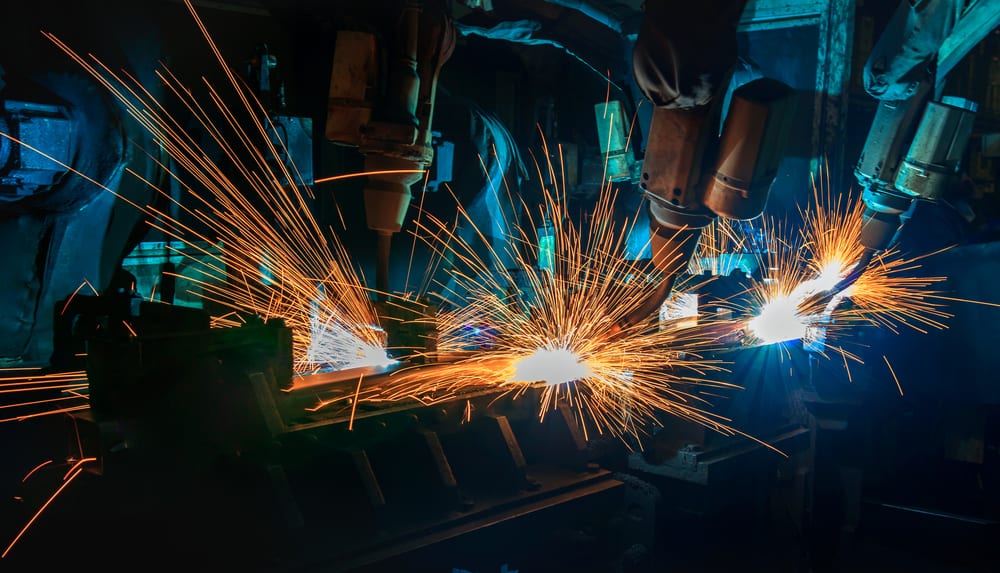
Types of Orbital Welding Processes
Orbital welding was designed specifically to address the inconsistencies of manual welding caused by human error and fatigue that can compromise weld quality. By automating the welding process, manufacturers can ensure the consistency necessary to meet quality standards and improve productivity. In high specification industries, orbital welding has replaced manual arc welding processes for applications where the tolerances do not allow for any errors and flaws are costly to repair. The quality and precision of the final weld are determined by the properties of arc, metal deposition, and weld cleanliness. The following are the most common orbital welding processes.
Gas Metal Arc Welding (GMAW)
This wire feed welding process utilizes an inert shielding gas such as carbon dioxide, argon, or helium to prevent weld contamination; the consumable electrode is fed wire continuously as it travels. Also known as Metal Inert Gas (MIG) welding, it is the most common form of wire feed pipe welding and is the fastest common welding practice. However, with unreliable and unpredictable sidewall fusion and penetration, GMAW is a gamble for high-specification projects and often requires reworking.
Flux Core Arc Welding (FCAW)
Utilizing wire with a core of flux as an electrode, the FCAW welding process is forgiving and offers welders more options to approach the weld. The flux core shields the weld from contaminants and is less easily disrupted by environmental factors. FCAW can be used in remote locations with little or no shelter from the outside environment. However, the flux core requires more amperage to start the arc than a gas shielded process like GMAW or GTAW, making it difficult to utilize FCAW for welding thin-walled materials. Excess heat can increase the chances of heat distortion, even in thick-walled stainless steels. And increased heat distortion during welding can make meeting specifications more challenging.
Gas Tungsten Arc Welding (GTAW)
GTAW welding utilizes a tungsten electrode that creates a narrow arc directed at the workpiece with an inert shielding gas preventing oxidation and other contamination during welding. The high degree of control in the welding process yields precise and consistent welds. Carefully controlled gas promotes weld purity that makes stronger welds. The process is also deployable in a variety of environments. With enough wind screening and forethought, operators can set up GTAW in an outdoor environment; this, however, is rare. However, compared to other welding processes, GTAW is complex and is difficult to learn. Mastering GTAW requires a great deal of practice.
Plasma Arc Welding (PAW)
Considered a more advanced type of GTAW welding, PAW uses two kinds of gas, one for shielding the weld and the other for generating plasma. Like the TIG welding process, plasma arc welding utilizes a tungsten electrode to create a plasma arc, generating heat. The benefit of plasma arc welding is the arc control that produces superior quality welds regardless of material thickness. However, the larger heat-affected area created by PAW (compared to TIG welding) can cause heat distortion or metal stresses that can weaken or ruin the workpiece. Also, the welding process utilizes large weldheads, limiting PAW’s range of environments.
Submerged Arc Welding (SAW)
As one of the older welding processes, SAW utilizes a continuously fed wire as an electrode, with the flux falling out of the hopper and burying the weld as it progresses. Although the process yields high-quality welds and is very fast, it is limited to welding in a fixed and, generally, flat position. Process immobility and increased material consumption mark the main disadvantages of SAW.
Laser Beam Arc Welding
This fusion welding process utilizes laser beams to join metal pieces. It is widely performed in high-volume applications using automation, such as the automotive industry. Because of its energy density, the laser beam arc welding process enables operators to melt the area located at the edges of the joint without affecting a large area. The high aspect ratio welds produced with a relatively low heat input compared to other arc-welding processes is one of the major advantages of deploying this welding process. However, laser beam arc welding is expensive, and the equipment size limits its usage to purpose-built environments.
Of the welding processes described, the GTAW process stands out. It offers a high degree of control over amperage and weld to produce pure-finished welds in high-specification projects. This can be credited to the flexibility of use that facilitates deploying the weld head and power supply where needed without requiring a special rig. The complexity of the welding process and the difficulty of finding skilled welders who have mastered this process can be effectively addressed through automated orbital GTAW welding.
Benefits of GTAW Orbital Welding
In high-specification and critical projects, there is no room for error that might result in system failure. The reliability and safety provided by GTAW orbital welding in such projects minimize human error while producing consistent, high-quality welds to meet specifications. The key benefits of GTAW orbital welding are:
Outstanding Purity
GTAW orbital welding produces high-quality, pure welds free from contamination by atmospheric oxygen, hydrogen, or nitrogen, making GTAW orbital welding ideal for applications that require hygiene and purity.
Consistency
In automated GTAW orbital welding, the weld head travels steadily and consistently, ensuring high-quality and repeatable welds.
Improved Productivity
With higher quality welds, automated GTAW welding improves productivity by reducing rework and damaged material costs in high-specification, low tolerance environments.
The benefits of GTAW orbital welding are attributable to the elements deployed in the welding process that improve the manual GTAW welding process and allow welders to create continuous welds.
Elements of Orbital Welding System
Weld consistency depends on several factors, including feed rate, current, and arc distance. Key elements of the orbital welding system—such as the power supply and weld heads—make pure and consistent welds achievable.
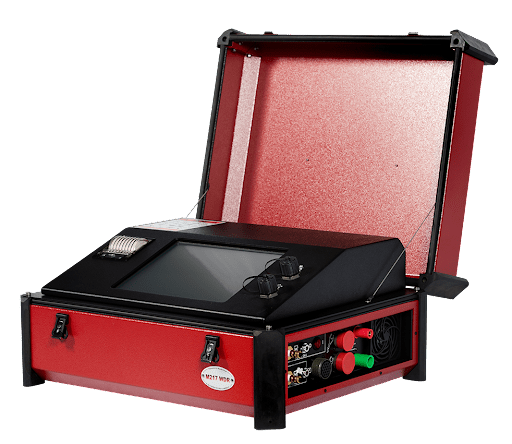
Power Supply
Weld parameter control is facilitated by the welding power supply that converts electrical power into the suitable current type required for the weld. The DC power supply is suitable for welding ferrous metals such as steel. AC power supply, on the other hand, works better when working with aluminum. For GTAW orbital welding, the power supply system includes power inverters and control tools that optimize the amperage, voltage, and polarity needed for the weld. Modern power supply systems deploy IoT and advanced analytics to capture data during the welding process and offer advanced programming options to analyze data, optimize specifications, control weld schedules, and monitor progress.
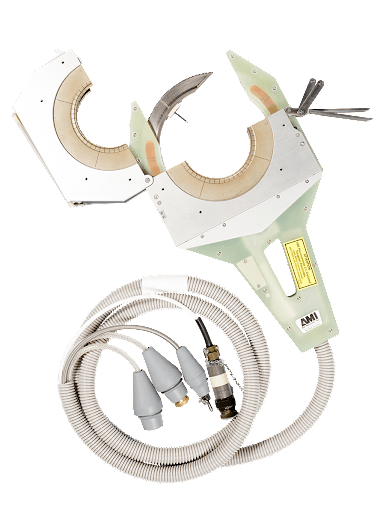
Orbital Weld Head
A critical component of the orbital welding system, the weld head rotates the arc 360 degrees around a stationary workpiece. Once connected to the power supply system, weld heads can perform the weld to fulfill programmed parameter specifications. Automation allows for multiple welds to be performed according to the exacting specifications of the schedule without errors due to operator fatigue or oversight. Welding data collected through the power supply can help operators detect errors and can be analyzed to improve the weld schedule in the future. Additionally, different weld heads can be used for different material thicknesses, geometries, and orientations.
Large Diameter Weld Head
The large diameter—or open—weld head can be clamped or mounted to a guide ring attached to the workpiece. Predominantly used for pipe welding, the large diameter weld head uses filler wire to perform the weld after multiple passes.
Small Diameter Weld Head
The small diameter—or closed—weld head is best suited for tube welding applications that demand hygiene and high-quality welds. The compact design of smaller diameter weld heads provides an inert atmosphere around the workpiece with high gas shielding to yield precise and clean fusion welds.
Additionally, advanced weld heads provide optimized, cost-effective solutions for interior and exterior diameter cladding; these weld heads also enable welding in unusual environments such as underwater or outer space. For example, the Model 15 large diameter weld head offers GTAW welding for all pipe sizes from 3 inches (76 mm) up—including flat plate. These advanced weld heads with automated robot arms facilitate the adoption of GTAW orbital welding for field use applications in nuclear, shipbuilding, petrochemical, and construction industries.
GTAW Orbital Welding Across Industries
An automated orbital welding system ensures greater precision and higher productivity. By addressing the inconsistencies of manual arc welding, orbital welding provides precise and consistent welds for sensitive pipe and tubing projects in various industries.
For example, in aerospace and petrochemical industries, stringent engineering standards for pipes and tubing can be effectively addressed through orbital welding to improve precision and reduce rejection rates. GTAW orbital welding yields pure, consistent welds with thorough penetration and fusion that improves the structural strength and product quality of pressure vessels for high-specification projects. For food-grade or pharmaceutical applications, orbital welding yields smooth surfaces without crevices to restrict microbial growth and prevent product contamination. The advantages of orbital welding have been realized across almost every major industry, including semiconductors, nuclear, power generation, shipbuilding, construction, and more.
Arc Machines has a long history of designing, developing, and manufacturing specialized orbital welding equipment for specific applications. Precise GTAW orbital weld heads and power supplies facilitate:
- Tube-to-tubesheet welding
- Narrow groove welding
- Interior diameter cladding
- Weld overlay cladding
- Filler or socket welding
- Butt welding
With a 100-percent duty cycle to provide peak performance for extended periods without compromising weld quality, the equipment meets the requirements for the most demanding welding jobs. AMI’s extensive experience designing custom and commercial equipment enables various industries to adopt GTAW orbital welding for diverse applications.
READY TO CONNECT?
Arc Machines, Inc. is an industry leader in GTAW orbital welding for high-specification projects. For inquiries regarding our products, contact sales@arcmachines.com. For service inquiries, contact service@arcmachines.com. Contact us to learn more about our orbital welding solutions.