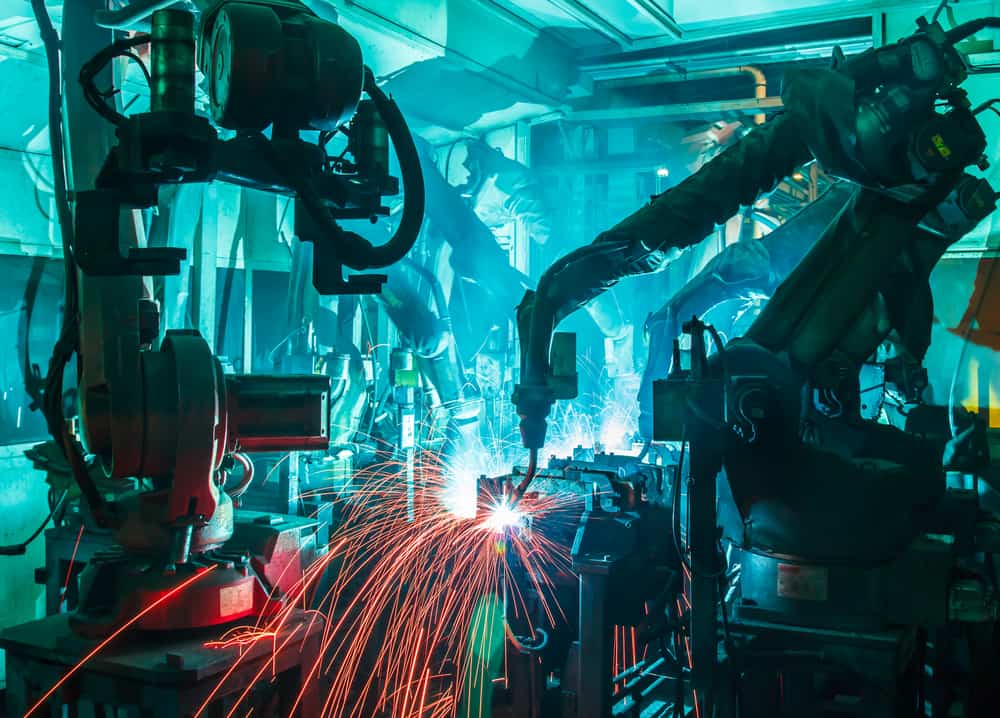
Technological updates should simplify operations, increase productivity, and reduce costs for manufacturers. Robotic welding has allowed industries to realize these benefits by shifting welding tasks from operators to smart automated robots. With accurate programming, operators can ensure optimal robot performance and incomparable weld results. Traditionally, robots have been programmed on-site…