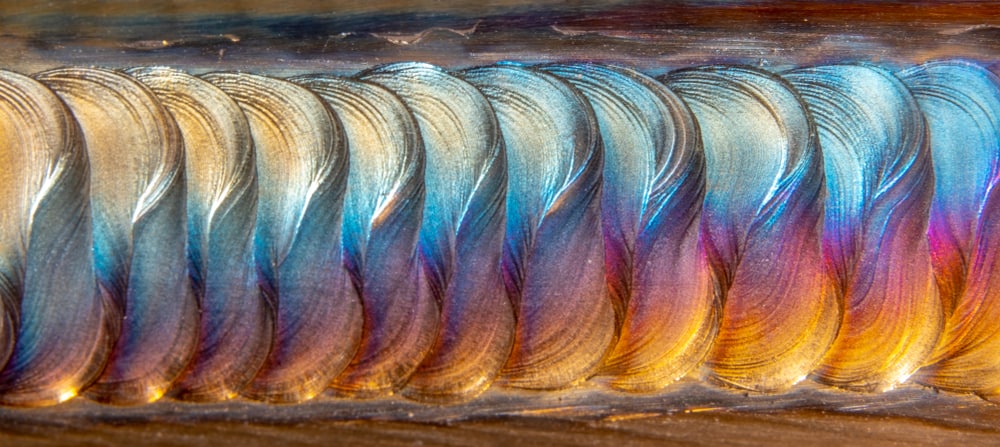
If you are performing a welding operation, you’re familiar with the term “purging,” which is simply the method of extracting oxygen from the welding scene to avoid the risk of oxidation. When TIG welding, purging prevents issues like pitting, cracking, and splatter from arising. Argon, the most notable purging gas,…