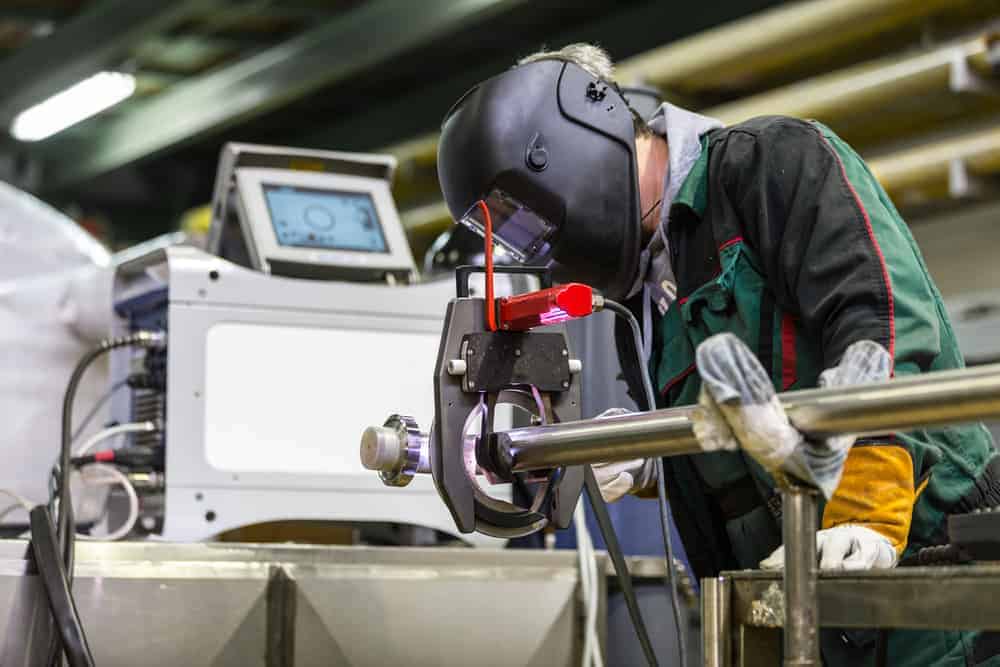
Welding terminologies can seem broad and confusing even to those with several years of welding experience. If you are interested in welding or a career in orbital welding, it is important to know the basics. We are here to help. Although technicalities across manual welding and orbital welding may differ,…