The Food and Drug Administration (FDA) has established the Food Safety Modernization Act (FSMA) to help industries make certain that final products are not contaminated. To ensure good hygiene and sanitation during food production and handling, industries should adhere to welding standards for each component that impacts processing. Additionally, welders fabricating equipment, tubes, and pipelines should possess a thorough understanding of food-grade welding regulations, as well as the best tools to perform hygienic and sanitary welds that will minimize potential risks to public health.
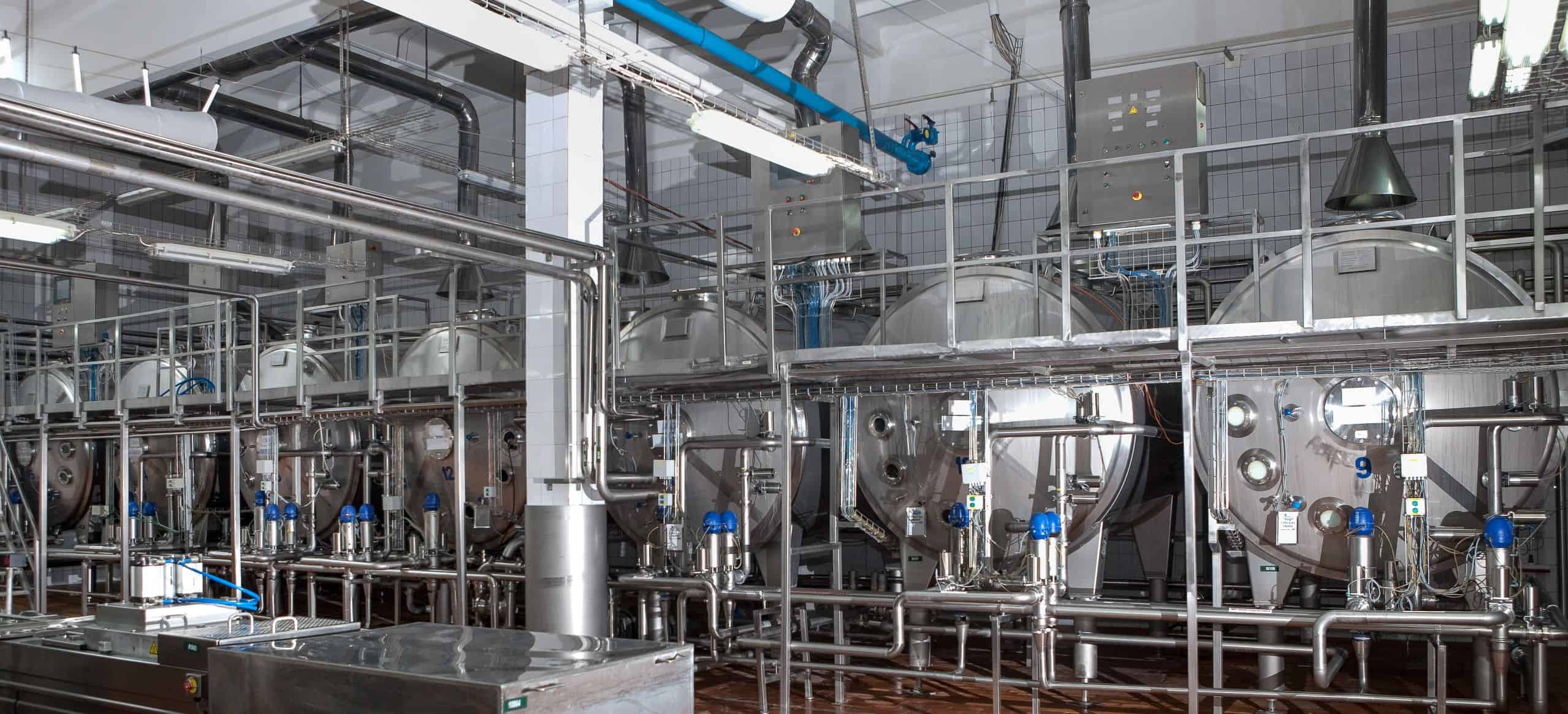
Challenges for Safe and Sanitary Welding
Food-grade welding should prevent contamination. To do so, the industry generally uses corrosion-resistant and highly durable stainless steel as its point-of-contact material. In welding stainless steel or other materials used in the food and beverage industry, welders should be mindful of the following practices that encourage welding precision:
- Employ precise weld parameters when welding stainless steel to ensure the corrosion-resistant oxide layer is intact.
- Eliminate excess stress and overheating to reduce the chances of stress-corrosion cracking.
- Use the correct filler material to promote a strong bond, weld strength, and integrity.
- Avoid welding dissimilar metals to reduce the risk of heat stress cracking and corrosion caused by different thermal capacities.
- Eliminate burrs, cracks, and corrosion to reduce the risk of food contamination and bacterial growth.
Maintaining Food Grade Standards
The FSMA requirement, signed in 2011, aimed to regulate manufacturers and handlers in the food and beverage industry and increase good welding and manufacturing practices. The comprehensive standard outlines the following guidelines:
- Stainless steel must have a minimum chromium content of 16 percent to obtain the food contact substances approval.
- The surface roughness of the component must not be greater than 0.8µm (0.008mm) or 30 micro-inches. Any burrs or sharp edges should be eliminated from the welded surface. Electropolishing or sanding can be used to smooth out the welded surface.
- The weld should be properly performed to avoid the formation of cracks or pores on the surface as they can trap the food material and be the source of bacterial growth.
- The welding surface should be properly cleaned.
The many advantages of orbital welding can make it easier for manufacturers to achieve these varied welding requirements.
Food Safety With Orbital Welding
Automated welding systems such as orbital welding can help ensure your welds meet the safety and hygiene required for the food and beverage industry. Orbital welding employs a controlled and precise process that facilitates weld parameter controls which allow for precision weld standards. Additionally, an automated weld head and remote monitoring system can help eliminate human error and enable real-time weld process monitoring. An orbital welding process and proper knowledge of food-grade welding requirements allows industries to efficiently maintain the integrity of their food processing systems and minimize the health risks resulting from contamination.
READY TO CONNECT?
Arc Machines, Inc. is a leader in orbital welding technology that offers experience and expertise to help you maintain your safe and precise food-grade welding requirements. For inquiries regarding products, contact sales@arcmachines.com. We look forward to providing the equipment and services your project needs. Contact us today to learn more.