Manufacturing in a food-grade environment requires strict adherence to sanitary standards. While industries may achieve food-grade standards by maintaining material and product compatibility, weld joints are sometimes weak points. Therefore, it is crucial that welders familiarize themselves with the standards related to welding food-grade stainless steel pipes. To achieve these standards and meet the benchmark for quality and precision, many welders have turned to the automation and efficiency offered by orbital welding.
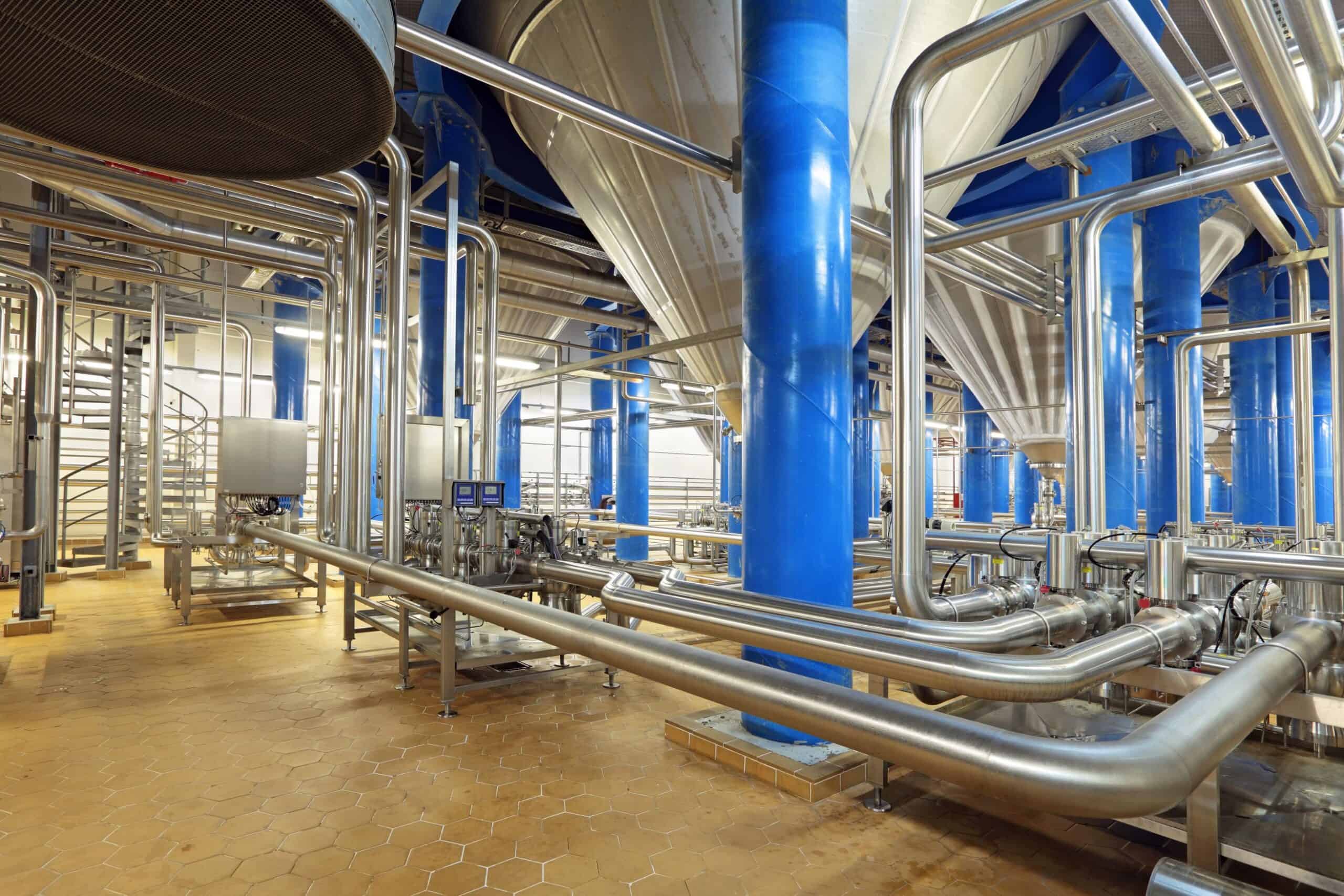
Food Grade Standards of Stainless Steel Welding
The food and beverage industry must adhere to the stringent Food Safety Modernization Act (FSMA) established by the Food and Drug Administration (FDA) to ensure food products remain uncontaminated during production and handling. To meet the FSMA standards, most tubes and pipes directly contacting the product are composed of stainless steel, which offers attributes including corrosion resistance, strength, and a smooth surface for easy sanitary maintenance.
However, apart from general weld requirements, such as proper surface preparation and elimination of cracks and porosity, welding food-grade stainless steel is accompanied by additional guidelines that include the following:
Meeting these standards for welding food-grade stainless steel requires a thorough consideration of weld parameters, filler materials, and welding processes. An automated welding system can help.
Meeting the Modern Standards in Welding Food Grade Stainless Steel
Automated welding processes like orbital welding enable manufacturers to effectively and efficiently meet industry welding standards. An automated system allows:
- Optimization of parameters such as voltage, current, arc length, and feed speed to achieve accuracy and precision in welding.
- Possibility of remote monitoring in welding stainless steel that helps to minimize hexavalent chromium exposure.
- Controlled heat input for increasing corrosion resistance and improving fusion of filler materials.
- Minimization of burrs to reduce the risk of bacterial growth and contamination.
Utilizing these benefits of automation for welding food-grade stainless steel pipes and tubes, the food and beverage industry can achieve quality standards. The controlled process enables food manufacturers to eliminate challenges and attain modern food production standards.
Orbital Welding: Maintaining Food Quality and Safety
Mechanized welding systems such as orbital welding have supported many industries in their efforts to meet industry-specific welding requirements. In the food processing industry, orbital welding can help ensure sanitary operation. These optimized systems allow manufacturers to control parameters such as heat or rate, allowing the system to perform precise welds without creating issues like cracks, porosity, or lack of fusion. By preventing these defects, manufacturers can maintain the integrity of the production system while eliminating potential contamination risks.
READY TO CONNECT?
Arc Machines, Inc. offers experience and expertise as a leader in orbital welding technology to help you meet the standards for welding food-grade stainless steel. For inquiries regarding products, contact sales@arcmachines.com. We look forward to providing the necessary equipment and services your project. Contact us today to learn more.