Technological advances are extending the welding profession—especially in orbital welding where automation, remote control, and monitoring are enabling technicians to create constant high-quality TIG welds at the level of experienced professionals. This level of precision and reliability is required for high-spec projects. In some cases, substandard or bad welds are unrepairable and can lead to unnecessary time and cost expenditures.
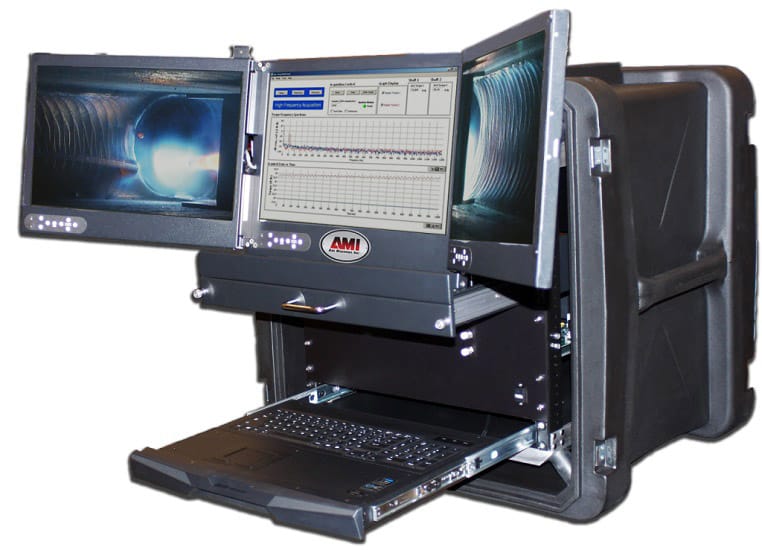
Therefore, not only is it important that you utilize the best process, equipment, and materials, but you should also have exceptional support to ensure minimal downtime for your high-spec projects. Arc Machines, Inc. (AMI), a leader in providing the most advanced and highest quality equipment for nearly 50 years, also supplies exceptional service and support to help you realize your vision.
The Advantages of Orbital Welding for High-Spec Projects
For large scale projects in industries such as aviation, power generation, and food and biopharma, quality and precision requirements are more stringent. Efficiency and cost control are also at a premium on these types of high-spec projects. Therefore, GTAW is the preferred welding process. And to ensure the required level of high-quality weld consistency, orbital welding is the best implementation choice.
Advantages of Orbital Welding
- Higher productivity
- Higher-quality welds
- Safer process
- More cost-effective
- Less physically demanding
To maximize these advantages, AMI provides orbital welding service equipment, materials, and support for your implementations.
AMI’s High-Spec Orbital Welding Service
To ensure that you are prepared to meet the requirements for your high-spec project(s), AMI offers comprehensive solutions that include advanced equipment, quality materials, and superior service.
Advanced Equipment
- Complete Orbital Welding Systems
- Weld Heads
- Wire Feeders
- Remote Control Pendants
AMI continues to raise the bar for welding quality, reliability, and efficiency by providing the most advanced orbital welding service equipment for purchase or lease. This includes weld heads, wire feeders, remote control units, and complete, ready-to-go systems.
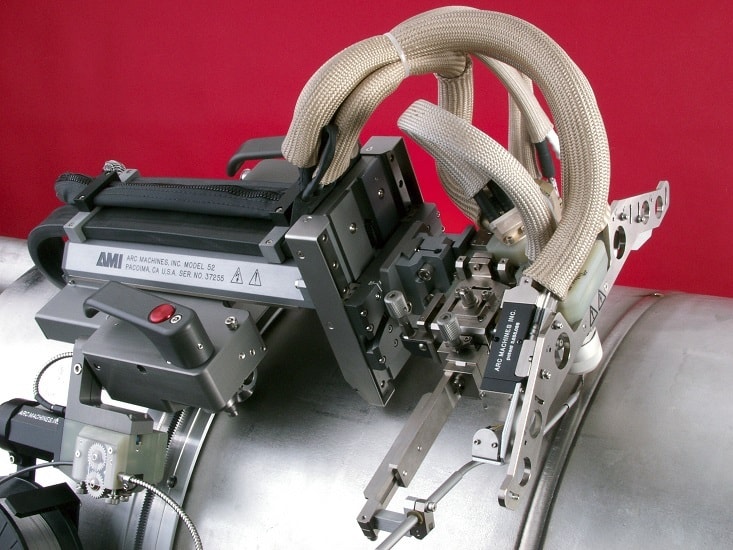
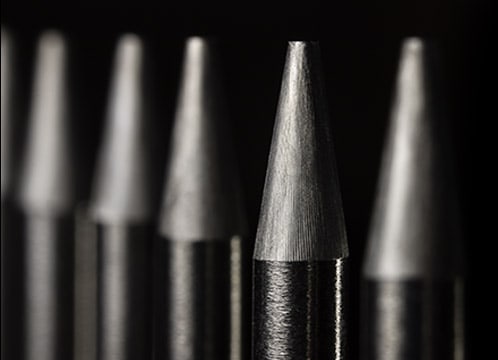
Quality Materials
- High-Purity Electrodes
- Custom Backcasted Narrow Groove Tungsten (NGT) Electrodes
AMI also provides the highest quality of tungsten electrodes in the industry. And for NGT applications, AMI offers custom backcasted narrow groove tungsten electrodes.
Superior Service
- 24-hour Phone Support
- Personalized Guardian
- Onsite Repairs and/or Replacements
- Remote Calibration and Testing
To keep your orbital welding equipment running at peak performance, a maintenance schedule that incorporates a daily checklist and scheduled preventive maintenance should be developed and followed. AMI support professionals are there with you for any issues that may arise. We also offer a Guardian service that pairs a dedicated service professional with your company for ongoing consultation and support.
AMI can perform repairs and/or replacements at your site or remotely. Additionally, regularly scheduled equipment calibrations can be correlated with your project schedule. In some cases, we also provide rentals or lease substitutes to prevent any downtime for your job while we perform maintenance on your equipment.
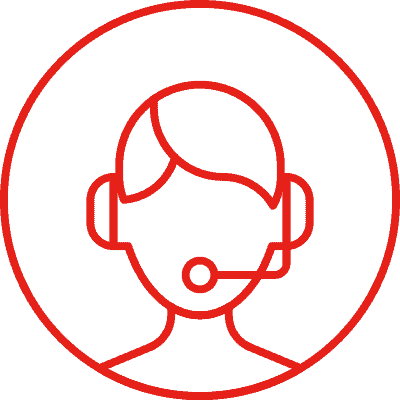
At AMI, we provide the complete orbital welding system solution to meet your high-spec assembly project needs.
READY TO CONNECT?
Arc Machines, Inc. specializes in high-quality, precision GTAW welding and has been a leader in advanced welding technology processes and equipment since its founding by former NASA engineers in 1976. We also offer a range of service and support solutions to ensure that you get the most from your orbital welding system. For inquiries regarding products, contact sales@arcmachines.com. For service inquiries, contact service@arcmachines.com. Arc Machines welcomes the opportunity to discuss your specific needs. Contact us to arrange a meeting.